Introduction
The market demands for higher productivity and lower costs have led biopharmaceutical contract manufacturers (CMOs) to investigate and adopt new, sometimes disruptive, process technologies. CMOs continue to invest in upstream and downstream process technologies to meet these demands. Adoption of new process technologies, such as higher titer expression systems, single-use bioreactors, and downstream purification technologies are seen as potential disruptive technologies. The successful implementation of these technologies will improve product quality, lower costs, and reduce cycle-times. For CMOs these technologies may significantly change the market for contract manufacturing services.
Disruptive Technologies
The concept of disruptive technologies was introduced by Clayton M. Christensen who describes technologies as either sustaining or disruptive [1]. The concept of sustaining versus disruptive technologies is different from the concept of incremental versus radical technologies. Most new technologies foster improved product performance. These sustaining technologies follow a path of improvements valued by the established customers in an industry. Disruptive technologies generally bring a different value proposition to the market and result in product performance that is initially worse than the accepted technology. The introduction of new process technologies in upstream and downstream biomanufacturing has the potential to be disruptive to the biopharmaceutical contract manufacturing industry.
Our Study
The adoption of disruptive technologies by CMOs is documented in HighTech Business Decisions’ recent report Biopharmaceutical Contract Manufacturing: New Participants, Expanded Services and Emerging Markets. For our study, biomanufacturing directors at pharmaceutical and biotechnology companies were asked about what disruptive technologies they see for biomanufacturing. Overall, slightly more than three-quarters of the biomanufacturing directors did see the presence of disruptive technologies in biomanufacturing. For the biomanufacturing directors who did not see the presence of disruptive technologies, most of them classified new biomanufacturing technologies as sustaining technologies rather than disruptive (Figure 1). Of the biomanufacturing directors who noted disruptive biomanufacturing technologies, 62% of those biomanufacturing directors see the use of disposables technologies as disruptive, while 24% mention high expression cell lines as disruptive (Figure 2). Other technologies mentioned by the biomanufacturing directors that may be disruptive include the use of transgenics (both plant and animal), the use of perfusion bioreactor technologies, multiplex protein synthesis and accelerated bioburden assays. These other technologies have the potential to be disruptive, but their successful adoption appears to be further into the future. 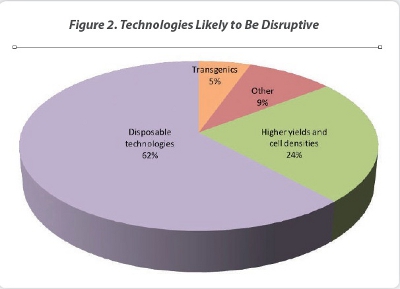
Single-Use Bioreactors
Many CMOs are expanding capacity with single-use bioreactors. Interestingly, CMOs who have extensive stainless steel bioreactor capacity are also making investments in single-use bioreactors. CMOs such as Fujifilm Diosynth Biotechnologies (www.fujifi lmdiosynth.com) and Boehringer Ingelheim (www.bioxcellence.com) are examples of two CMOs who are installing single-use bioreactors. Both CMOs have an extensive base of installed stainless steel bioreactor capacity. The advantages for of single-use bioreactors include reduced upfront investment in plant and utilities, which makes it economically feasible to add capacity in smaller increments, thus allowing a CMO to better match supply and demand.
As explained by Steve Bagshaw, managing director at Fujifilm Diosynth Biotechnologies, “We definitely see increased use of disposable technology in the mammalian cell culture space as a disruptive technology. It has the potential to reduce the entry barrier to manufacture of biologics through making a significant reduction in plant capital cost.” Improvements in cell expression systems have also contributed to the adoption of single-use bioreactors by obviating the need for ultra large-scale bioreactors that many biomanufacturing directors had expected they would be need for many of the biopharmaceutical projects currently in the pipeline. Thus while, improvements in yields and titers may be considered sustaining technologies, it has made it possible to use smaller-scale disposable bioreactors for larger scale projects. As noted by Mr. Bagshaw, “It [the adoption of single-use bioreactors] runs congruent with other factors such as higher cell line titers, which means that quantities that might previously have been only possible at greater than 10,000 L-scale become possible at 2,000 L- or 1,000 L-scale. These lower scales further reduce facility costs by reducing the overall size, reducing the scale of utilities needed and through changes in technology that become possible, such as the replacement of complex high cost capital equipment (including centrifuges) with simple, low cost disposable depth filtration.” Boehringer Ingelheim is also adding single-use bioreactors to complement its stainless steel bioreactor capacity. “The single-use bioreactors with a capacity of up to 500 L will be implemented and also available within the BI-HEX® platform. We offer this technology under both non-GMP and GMP conditions for preclinical and clinical trials, respectively,” said Dr. Julia Knebel, Director Marketing and Communications Contract Manufacturing Business, Biopharmaceuticals at Boehringer Ingelheim. “For a cost-effective campaign, Boehringer Ingelheim offers processing from stainless steel to full disposable as well as any hybrid combinations.
” Other benefits of disposable technologies include reduced risk of crosscontamination and lower validation costs. “In our GMP manufacturing facility, Wuxi AppTec has established a disposable production line to minimize the cross-contamination between products and reduce the number of annual validations required for maintaining cGMP compliance. The use of single use technology also allows WuXi AppTec to keep costs low,” said David Fischer, Business Development Manager, Protein Therapeutics at WuXi AppTec (www.wuxiapptec.com).
Analytical Tools
Another potentially disruptive technology being adopted by CMOs is the adoption of quality-by-design (QbD) principles, which is driving the adoption of new analytical tools and techniques. “The demands from QbD and biosimilars for more analytical data will create new bottlenecks, then the data from biosimilars in the clinics and on the market will open new levels of understanding of different types of contaminant profiles,” Dr. Knebel said. “Boehringer Ingelheim is very active in developing and implementing high-throughput analytical tools to not only drive development decisions more effciently, but also to impact decisions earlier in the development process.”
Wacker Biotech GmbH (www.wacker.com/biologics) recently implemented high-throughput screening processes to reduce their clients’ project timelines. “Due to the higher demand for our secretory E. coli technology ESETEC®, we have implemented a high-throughput screening process for the fast analysis of multiple producer strains and cultivation conditions,” said Thomas Maier, Ph.D., Managing Director at Wacker Biotech. “Parallel cultivations in micro-liter scale are performed and can be run under fed-batch conditions. This feature enables a seamless scale-up to small-scale bioreactors to allow final strain selection and quickly start fermentation development.”
“Wuxi AppTec is applying the strategy of Quality-by-Design to control the product quality and lower the cost from the clone selection stage to the end of fill-and-finish manufacturing,” said Mr. Fisher. “At the process development stage, Wuxi AppTec downstream is establishing a high-throughput screening platform to support clone selection and cell culture development to control the impurities profile of harvested material by assessing the risk of product related impurities on the downstream manufacturing process.”
Downstream Purification
As previously mentioned, the demands for higher productivity and lower costs have led CMOs to investigate and adopt new, sometimes disruptive, process technologies. One area of focus for CMOs is improvements to downstream purification processes, including the use of disposable technologies to replace such process steps as affinity chromatography and ion exchange. The need for improvements in downstream purification results in part from the work that led to higher cell culture titers over the past decade. In many instances, higher titers caused the biomanufacturing production bottleneck to shift to downstream purification; thereby, reducing the overall benefits available from implementing higher titer processes. “The main driver for innovation in downstream processing is the higher productivity obtained with novel expression technologies for both mammalian and microbial-based protein production,” Dr. Maier, said.
To address this issue, CMOs are investigating and investing in downstream purification technology, including various downstream disposable technologies. A few CMOs note that some of these new downstream technologies are already available, while other technologies are still in development. Below are examples from two CMOs and their suppliers of technologies being developed for downstream purification.
“A fully disposable process is one of the technology areas that has been fully evaluated and is no longer a future technology but more a present reality,” Dr. Knebel said. “Alternative technologies to chromatography are also very much in focus. Recent advances in membrane technologies such as membrane adsorbers are having an impact throughout the purification process. In the near term, membranes will improve the efficiency and effectiveness of process based impurity removal such as virus and DNA removal, but in the future, may also impact specific product-based impurity removal.”
EMD Millipore (www.emdmillipore.com) offers adsorber technologies for downstream purification. ChromaSorb™ membrane adsorber is a single-use, flow-through anion exchanger that replaces the traditional polishing steps in downstream purification. This technology results in significant savings to the CMO. “In the past, using this type of membrane technology for purification required large amounts of buffer, which became a rate limiting step,” said Conrad Maher, Product Manager at EMD Millipore. “ChromoSorb™ maintains capacity at high salt concentrations (by as much as 80% depending on manufacturing conditions) over traditional chromatography.”
Gallus BioPharmaceuticals (www.gallusbiopharma.com) is partnering with others to deliver potentially disruptive downstream processing technologies. “Gallus is also working with innovative new technologies to improve the efficiency of downstream processing, such as deploying the single-use Natrix Separations, Inc’s Advective™ chromatography, which delivers scalable high-capacity separations from capture through final polish with significant potential improvements over conventional resin-based columns,” said Mark R. Bamforth, President & CEO of Gallus Biopharmaceuticals. “The single-use Natrix Separations, Inc’s Advective™ chromatography has the potential to be disruptive. The Advective™ technology combines the superior binding capacity of conventional resin-based columns with the high throughput of membranes in a single-use format that has the selectivity of chromatography, eliminating costly packing, cleaning, validating and other burdens of conventional methods.”
Technical Challenges
There continues to be technical challenges with the adoption of disposables noted Mr. Bagshaw. “There are a number of technical challenges to be worked through including how chromatographic separation is handled in disposable formats, extractables and leachables understanding etc, but incentives to develop practical solutions to these areas are very large. We see disposable technologies having an initial impact on platform-type mammalian processes, particularly mAbs. A particularly interesting technical challenge, which is still to be solved for disposable technologies, is its application to microbial systems with their higher heat and mass transfer requirements.”
Despite these technical hurdles in downstream processing, the benefit for the successful adoption of these technologies provides an incentive for CMOs to invest resources to develop and implement these processes at their facilities. These benefits include lower facility and utility capital costs, along with productivity and quality improvements.
Conclusion
Most biomanufacturing directors see the adoption of disposable technologies and higher titer cell lines as being disruptive technologies for biomanufacturers. CMOs are most likely to benefit from the successful implementation of these disruptive technologies, given the competitive demands in the market place for improvements in quality, cycle time and costs. These trends are driving CMOs to investigate and invest in these new process technologies. Both large and small CMOs are investing in single-use bioreactors, with established CMOs investing in single-use bioreactors to complement their extensive stainless steel bioreactor capacity. CMOs are also investigating and implementing various downstream purification process technologies. New process technologies such disposable membrane adsorbers and disposable chromatography columns are being investigated and have the potential to be a disruptive technology.
References
Clayton M. Christensen, The Innovator’s Dilemma When New Technologies Cause Great Firms to Fail, (Boston: Harvard Business School Press, 1997).
William Downey, MBA is President and Helen Nicely, Ph.D. is Senior Market Research Analyst at HighTech Business Decisions, a market research and consulting firm. HighTech Business Decisions publishes the comprehensive industry study, Biopharmaceutical Contract Manufacturing: New Participants, Expanded Services and Emerging Market, which is based on interviews with 70 executives at pharmaceutical and biotechnology companies, and contract manufacturing organizations. (408-978-1035, www.hightechdecisions.com).