Hiring problems, and finding experienced technical and production staff have biomanufacturers worried about production bottlenecks this year. According to our 8th Annual Report and Survey of Biopharmaceutical Manufacturing Capacity and Production, we found that among 352 industry respondents, 31% consider hiring concerns are likely to result in production capacity constraints over the next five years [1]. After declining from 2008 to 2010, the factor has once again become a widespread concern, trailing only “facility constraints” – which leads with 49% of biomanufacturers indicating. To prevent bottlenecks, better recruiting and hiring of operations staff will need to occur. Although the issue is growing again, worries about finding and hiring technical and production staff have not reached the levels seen in 2004, when it was the #1 concern, cited by 52% of respondents.
Our survey, which includes respondents from biomanufacturers in 31 countries, asked about the major factors likely to constrain their organization’s production capacity over the next five years. Training is part of the solution identified by industry experts. According to Dr. Rick Johnston, CEO of Bioproduction Group Inc., “Recent contamination events in the industry have… highlighted the need for hiring and retaining experienced scientific staff that have experience in cell culture and purification, as well as operating technologies like pasteurization and disposables. [1]" This trend indicates the industry is shifting toward sustained, efficient commercial operations rather than the scramble to build new capacity seen in the early 2000s.
Indeed, concerns about staffing appear to have increased, when compared to 2010, in other areas as well: For example, the #4 Factor: ‘Inability to hire new, experienced scientific staff’ (27.6% of respondents this year compared to 19.1% in 2010); and the #8 Factor: ‘Inability to retain experienced scientific staff’ (20.5% this year compared to 17.2% in 2010).
In this year’s #3 slot, “Physical capacity of downstream purification equipment” is not as much of a worry to the industry, with only 28% of respondents indicating this as a future constraint factor, down from 42% in 2010. Rounding out this year’s top 5, “Analytical testing and drug product release’ also fell, from 31.9% of developers in 2010 to 26.2% this year.
Overall, this year we found only 14.3% of respondents indicating they are “unlikely to see capacity constraints in the next 5 years.” This is up from 10.3% last year, but still down from 21.4% and 22.7% in 2009 and 2008 respectively.
The increased focus on hiring and retaining talent in this year’s survey is reflective of many factors, including: need for experienced operators to mitigate contamination risks; increasing shifts to maximize capacity within facilities without capital outlay on new equipment; and a focus on driving operational excellence to reduce costs and cycle times. All of these initiatives require skilled individuals with a depth of production experience.
Gaps Emerge Between CMOs and Their Clients
We evaluated responses from biotherapeutic developer vs. CMO, and found, in general, that developers were more concerned with productivity and analytical testing, while, CMOs have much greater concern for hiring and employee retention. This reflects their closer attention to process and operational issues, where a host of operational improvements are needed in the short term to lower costs while increasing production efficiency. Experienced individuals are important in driving and sustaining these improvements.
Outsourcing of Services Affected by Hiring Trends
Our study also reveals that biopharmas see outsourcing as a useful tool that can have direct impact on their overall business strategy. We found that the industry outsourced increasing percentages of core capabilities such as upstream process development, typically an in-house activity. This may signal increased integration of outsourced services to come.
Indeed, our data shows that while hiring lags, outsourcing of services is increasing almost across the board. This year, of 23 different areas of outsourcing tested, two of the top three were service related. We asked biomanufacturers which areas they were outsourcing at least some activity today, finding that 69.3% of sponsors outsource some validation services (compared with 64.3% last year). These were marginally behind product characterization testing (70.0%) as the dominant outsourcing activity. At the other end of the scale, there appears to be relatively low outsourcing activity for Design of Experiments, and downstream process development.
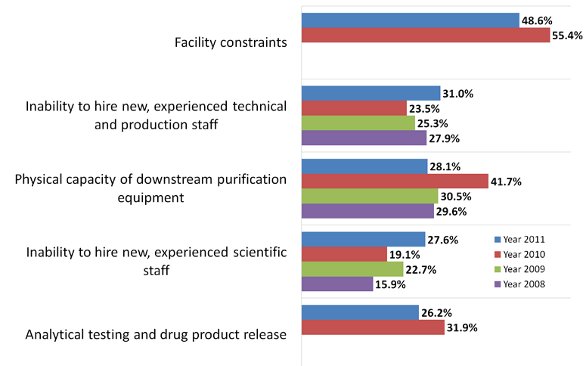
Figure 1 - Selected Results: Factors Creating Future Capacity Constraints, 2008-2011 What Factors are Likely to Create Capacity Constraints at Your Facility within 5 Years?
When comparing these results to 2010, we discovered that outsourced services have increased in most areas. For example:
- ‘Validation services’ (69.3% this year compared to 64.3% in 2010)
- ‘Environmental monitoring services’ (41.4% vs. 40.0%) pages.
- ‘Project management services’ (37.9% vs. 21.4%)
- ‘QbD services’ (26.4% vs. 19.3%)
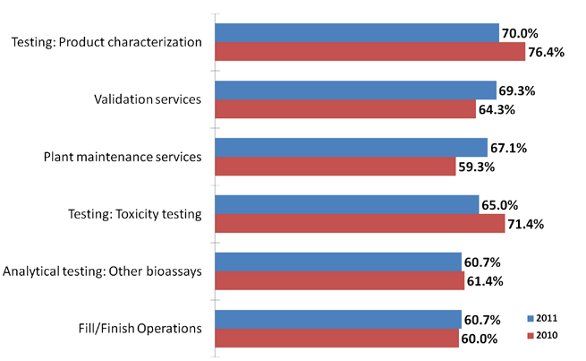
Figure 2 - Selected Results: Percent of Biomanufacturers Outsourcing at Least Some Activity Today, 2010 vs 2011
Indeed the most popular category to gain significant traction from last year’s results was validation services, which grew from 59.3% of respondents last year outsourcing some activity (good for the #6 spot) to 67.1% this year (the #2 spot). By contrast, the major testing activities experienced a decline from 2010: product characterization testing fell from 76.4% of respondents last year to 70.0% this year, while toxicity testing dropped from 71.4% to 65.0% of respondents.
Levels of Outsourced Services Also Increasing
The study also estimated the average percentage of outsourcing done by biomanufacturers today, and we found that, on average, facilities outsource just under one-quarter (24.6%) of their validation services. Not surprisingly, ranking at the top was “fill/finish operations” (#1 with 33.5% of the activity outsourced), followed by toxicity testing (#2, with 25.2%) and production characterization testing (#4, with 22%).
When comparing the responses to 2010, we found that once again the volume of outsourcing of services appears to be on the rise. For example, “validation services” rose to 24.6% this year compared with 20.7% last year. Similarly, regulatory services showed a slight increase (11.8% vs. 9.8%), project management services (9% vs. 5.9%) and QbD services (5.7% vs. 3.6%) also were outsourced at greater levels.
Will Outsourced Services Level Off?
While the data from our report plainly shows that outsourced services have increased, the outlook is not as clear. To identify where the greatest changes will occur, we asked respondents which activities they will be outsourcing more often in the future, specifically: “Which outsourcing activities will be done at significantly higher levels at your facility over the next 24 months?”
We found that 23% of biomanufacturers will be outsourcing significantly more ‘fill/finish operations’ over the next 24 months than is currently done, followed by ‘validation services,’ ‘downstream production operations,’ and ‘upstream production operations.’
However, when comparing responses to this question from 2010, the most significant changes were not found in services, but rather in upstream and downstream production operations. This year, downstream production jumped from 6th place (14.3%) in 2010 to 2nd place (22.1%), while upstream production’s leap was even more dramatic, from one of the least projected activities for growth in 2010 to the 2nd spot. Indeed, upstream production shows a projected near-tripling of the percentage of companies considering outsourcing these operations (8.6% in 2010 to 22.1% in 2011).
In contrast to the consistent increase in services being outsourced today, comparing this year’s projections for significant increases to 2010 yields a mixed bag. In fact, a number of common outsourced services now make up the bottom three activities in terms of projections for significantly higher levels of outsourcing in the next 24 months. This suggests that outsourced services may be hitting their peak this year, and will level off in coming years.
Outlook for Hiring and Outsourced Services
As many countries, including the US, move towards cost controls, the economic and political environment will continue to create pressures for cost-containment by governments and industry. Aging populations, fewer young workers entering the job market, and governments’ budget restrictions and inability to pay for high-quality health care for their citizens will all be contributing factors to a difficult economic environment.
A bright spot can be found in the continued growth of the biopharmaceutical industry, even while the world economy lags. It is also one of the few manufacturing industries where the U.S. and Europe can claim to be clear leaders. And yet, companies continue to cut back where they can, and outsource when they can. R&D will continue to be outsourced and offshored. CMOs can expect steady increases in their business. In the long run, offshoring based solely on cost-savings will likely decrease as host country costs, especially salaries and operational costs, increase. For the immediate future, though, it appears that relatively lower value-added services such as validation services will continue to be outsourced at greater levels, as companies cut back on budgets wherever possible and staffing concerns persist.
Reference
- 8th Annual Report and Survey of Biopharmaceutical Manufacturing Capacity and Production: A Survey of Biotherapeutic Developers and Contract Manufacturing Organizations, BioPlan Associates, April 2011, 490 pages.
Eric S. Langer is president and managing partner at BioPlan Associates, Inc., a biotechnology and life sciences marketing research and publishing firm established in Rockville, MD in 1989. He is editor of numerous studies, including “Biopharmaceutical Technology in China,” “Advances in Large-scale Biopharmaceutical Manufacturing”, and many other industry reports. [email protected] 301-921-5979. 
Survey Methodology: The 2011 eighth Annual Report and Survey of Biopharmaceutical Manufacturing Capacity and Production in the series of annual evaluations by BioPlan Associates, Inc. yields a composite view and trend analysis from 352 responsible individuals at biopharmaceutical manufacturers and contract manufacturing organizations (CMOs) in 31 countries. The methodology also encompassed an additional 186 direct suppliers of materials, services and equipment to this industry. This year's survey covers such issues as: new product needs, facility budget changes, current capacity, future capacity constraints, expansions, use of disposables, trends and budgets in disposables, trends in downstream purification, quality management and control, hiring issues, and employment. The quantitative trend analysis provides details and comparisons of production by biotherapeutic developers and CMOs. It also evaluates trends over time, and assesses differences in the world's major markets in the U.S. and Europe.